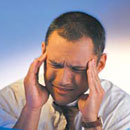
En muchas ocasiones se plantea la siguiente problemática: afrontar una mejora para un método que ya está en perfecto funcionamiento, pero “¿Entonces para qué el cambio?”. Este cambio puede significar un resurgimiento de una serie de problemas, como acabamos de ver, que no todos están dispuestos a afrontar. Este miedo al cambio es una barrera que debemos evitar. Una posible mejora está siempre justificada.
Por tanto ante la pregunta conformista de ¿Por qué? o ¿Para qué el cambio?, la respuesta optimista es siempre: - Para seguir el camino hacia la optimización. Esta optimización no sólo es recomendable sino también imprescindible para la supervivencia de nuestras empresas.
Entonces, ¿Por qué no se realizan estas mejoras?
Este ultimo punto es el que mas dificulta la implantación de las mejoras, frenando el avance hacia la excelencia empresarial. Debemos afrontar los cambios, luchar por la mejora continua, aunque cometamos errores. Si no nos enfrentamos al problema nunca lo solucionaremos.
Nadie esta en posesión de la verdad, pero tenemos y debemos conseguir que los problemas afloren para poderlos solucionar.
Analizar las situaciones y conseguir que los problemas salgan a la luz es la única forma de saber que tenemos un problema. Intentar solucionarlo, dar ideas, aunque contengan errores. El que no afronta los problemas, naturalmente nunca se equivocará, y seguramente será el primero en reprocharnos nuestra equivocación.
La frase “El análisis para la parálisis” es una realidad en nuestras empresas. No nos equivoquemos cuando vayamos a analizar un problema. Cuantas veces hemos visto análisis y mas análisis para solucionar un problema y nunca se termina de solucionar.
No busquemos la solución perfecta para todos nuestros problemas porque no la hay. Intentemos construir una lista de propuestas y soluciones para tomar la decisión que creamos mas acertada.
Hoy en día no podemos perder el tiempo en buscar soluciones milagrosas, no busquemos el milagro, busquemos la mejora, seguramente detrás de esa mejora veremos que aun es posible otra mas. Mejora continua, avanzar.
Construyamos desafíos, y hagamos realidad los cambios, aprovechemos el aprendizaje para crear innovación y mejora.
El camino a seguir para conseguir nuestras mejoras debe ser...
No olvidemos que la evaluación de los resultados va de la mano con la mejora continuada, si no evaluamos donde estamos nunca llegaremos a donde queremos ir.
La Autoevaluación por sí misma no aporta valor añadido, pero si detecta los puntos fuertes y todas las áreas de posible mejora.
En muchas empresas las autoevaluaciones no se basan en hechos reales que nos puedan permitir identificar y evaluar la organización del proceso productivo, mucho menos medir su avance.
Cambiar significa implantar las mejoras eficazmente bajo tres parámetros fundamentales; según su importancia, la urgencia y los recursos que necesitamos para su implantación y la actitud es la herramienta para conseguirlo.
En el sector industrial y en concreto en los procesos de fabricación, existen muchas ocasiones en el que se plantea la disyuntiva de afrontar un cambio que supone una mejora en el método del proceso productivo. Un método, que en muchas ocasiones ya funciona. Entonces, ¿por qué provocar un cambio? ¿Por qué buscar un conflicto en algún departamento de la empresa?
La reacción frente al cambio puede dar lugar a una serie de problemas que no todos los estados están dispuestos a afrontar. Desde el operario, que tiene que ejecutar las operaciones, hasta la alta dirección de la empresa, que debe dar el apoyo a ese cambio. Ellos se obligan a estar en sintonía para que los resultados sean satisfactorios. Se necesita un periodo de adaptación al cambio y un gran esfuerzo que en la mayoría de las ocasiones es recompensado con los resultados obtenidos.
Cuando se plantea la posibilidad de variar un proceso productivo afloran los problemas propios de rechazo, de adaptabilidad, de conformismo e incluso el “fantasma del estancamiento” del pasado sin unos planes específicos de progreso en el fututo. Todos ellos se presentan en el momento para impedir que las dificultades que surgen sean solucionadas de manera adecuada.
¿Por qué surge la problemática cuando se plantea el cambio?
Nadie en la empresa posee la verdad completa en cuanto al cambio y a los resultados finales que se obtendrán, por eso antes de emprender la carrera con firmeza y decisión es preciso medir las posibles soluciones en lugar de recoger opiniones genéricas de toda la compañía que no nos llevarán a nada.
El principio físico de inercia (Isaac Newton) indica que todo cuerpo continua en su estado de reposo ó movimiento uniforme y rectilíneo, si sobre él no actúa ninguna fuerza. Ese mismo principio físico se podría emplear para comprender la problemática que se plantea cuando aparece la posibilidad del cambio.
Imaginemos el departamento de Investigación, Desarrollo e Innovación (I+D+i), ayudado por el departamento de Ingeniería de Fabricación, de una empresa que ha conseguido obtener, después de meses de trabajo, una pieza que va solucionar todos los problemas visuales (no funcionales) que han surgido en un producto desde que se comercializa.
Los departamentos desde el principio no han hecho partícipes, en la medida de lo posible, a los operarios en el desarrollo de la nueva pieza y al llegar el momento de fabricar los primeros prototipos con la ayuda de las personas que van a trabajar con ella, les resulta completamente desconocida. ¿Cuál es la reacción?
Las miradas de extrañeza, el no saber como acoplar la nueva pieza y las observaciones como “lo que hago ahora siempre será mejor” surgirán desde las secciones del departamento de producción y nos harán reflexionar sobre todo lo que hemos dejado de hacer para que se produzcan estas reacciones.
La individualidad de la persona en oposición al equipo formado por toda la compañía aparece cuando no se les tiene en cuenta en los desarrollos que les afectan y no se dará cuenta que la pronta adaptación al cambio supondrá la mejora, no sólo del método, sino de uno mismo.
Los procesos fueron diseñados de manera que no existe un flujo de información entre los distintos departamentos. Los procesos se habían definido por cada uno de los departamentos habiendo diseñado procesos que pudieran dar lugar a ineficiencias cuando el proceso cruza varias áreas.
La naturaleza propia de las personas puede ser un duro escollo que hay que superar para lograr con éxito los cambios de métodos. Para ello es preciso tener un plan de formación en la empresa para concienciar a todos que somos el activo más importante y que la colaboración es fundamental. Los planes de actuación y el seguimiento personalizado de cada individuo de la empresa ayudará a mantener a un lado la dejadez, los conflictos personales y las reticencias a los momentos de cambio.
Por Ángel López Lubian, Responsable de Proyectos del Departamento de I+D de Flex Equipos de Descanso, S.A. y Rafael Domingo Arroyo, Jefe de Proyecto del Departamento de Ingeniería de Fabricación de Flex Equipos de Descanso, S.A., Masters en Dirección de Producción y Logística por IDE-CESEM.